Hamptons Engineering: Balancing Luxury with Coastal Realities
Designing and building luxury homes in the Hamptons comes with a distinct set of challenges—and opportunities. From the dunes of Montauk to the bluffs of Sagaponack Village, this stretch of Long Island’s East End is defined by its coastal beauty, charming communities, and increasingly complex site conditions. For architects and developers, delivering the high-end finishes,…
Frank Cuffaro
July 9, 2025
16 mins read
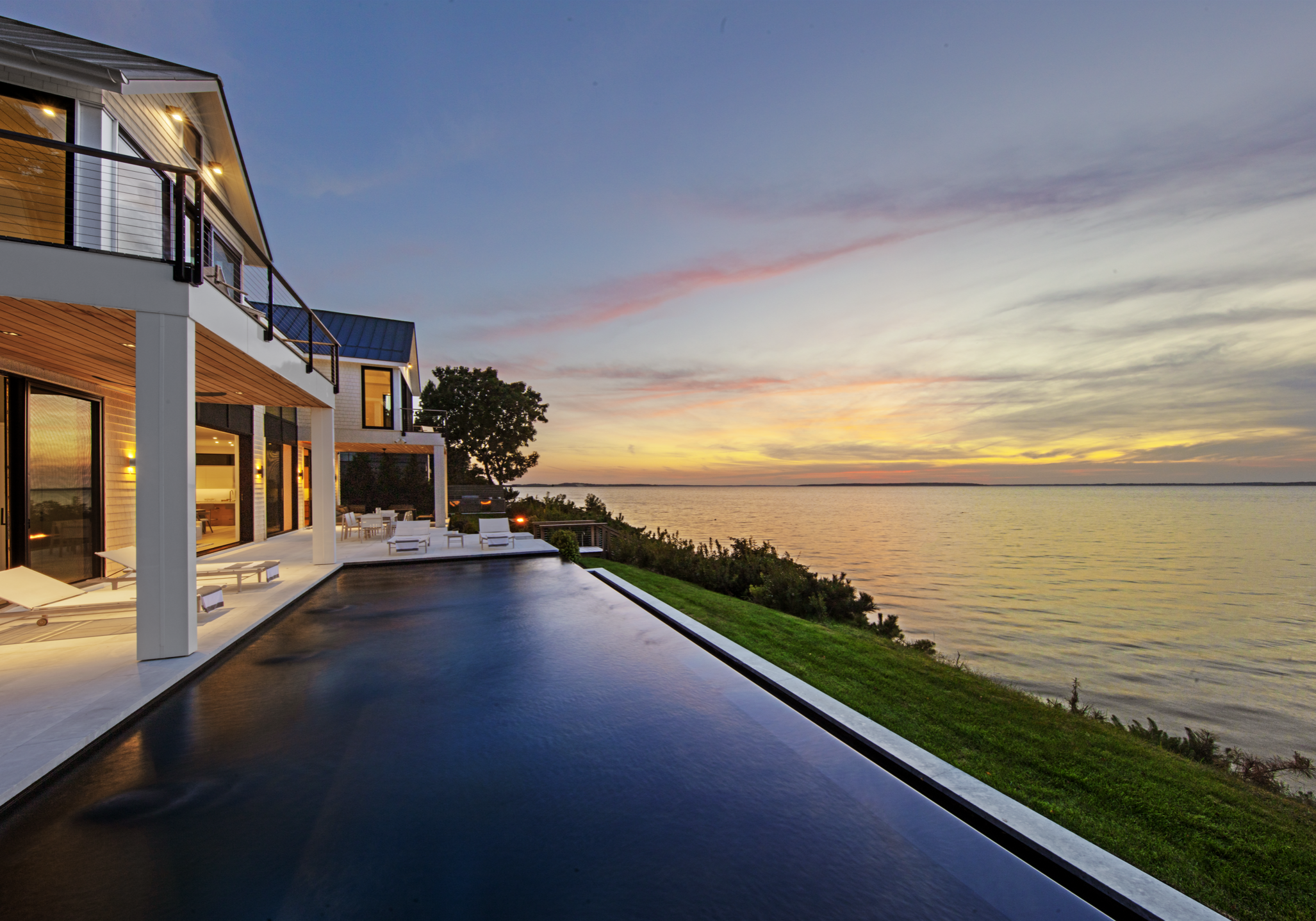
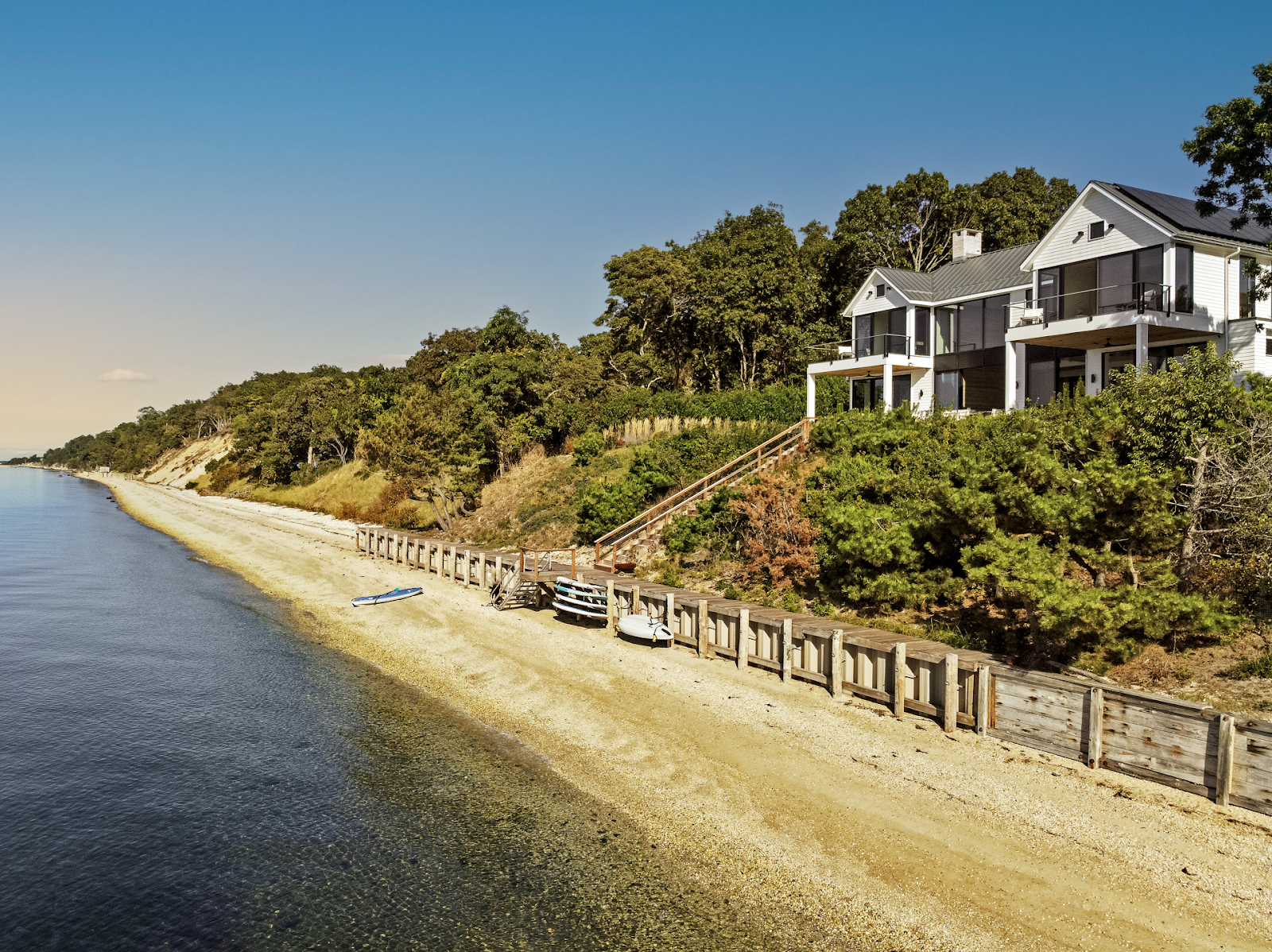
Designing and building luxury homes in the Hamptons comes with a distinct set of challenges—and opportunities. From the dunes of Montauk to the bluffs of Sagaponack Village, this stretch of Long Island’s East End is defined by its coastal beauty, charming communities, and increasingly complex site conditions. For architects and developers, delivering the high-end finishes, expansive spaces, and elevated comforts that homeowners expect requires an engineering approach that’s both highly technical and deeply collaborative.
At DiLandro Andrews Engineering, we’ve found that successful projects begin with a clear understanding of how architectural goals must align with engineering realities. Whether it’s supporting expansive open spaces with concealed structural systems, integrating high-performance HVAC into design-forward interiors, or fitting pools, septic, and utilities seamlessly on constrained sites, each discipline—structural, civil, and mechanical—plays a role in bringing these homes to life. These are not just code-compliant structures; they are finely tuned environments that demand engineering solutions as elevated as the homes themselves.
In this article, expanding on a recent Corcoran inhabit feature, we explore the key structural, civil, and mechanical engineering considerations for high-end residential construction in the Hamptons—and how working with an experienced engineering team can help bring sophisticated architectural designs to life.
Meeting the Expectations of Modern Hamptons Engineering and Architecture
High-end residential architecture in the Hamptons has evolved well beyond traditional beach cottages and shingle-style estates. Today’s homeowners are seeking modern, sophisticated designs that seamlessly blend indoor and outdoor living, maximize expansive water views, and deliver exceptional comfort year-round. For architects, this means pushing the boundaries of design while maintaining the refined, understated elegance that defines Hamptons living.
At DAE, we understand the pressures architects face to deliver on these expectations—without compromising performance, comfort, or durability. Some of the most common architectural priorities we see on the East End include:
Expansive open floorplans: Large, uninterrupted spaces with high ceilings and minimal structural interruptions are a hallmark of Hamptons homes. Achieving these dramatic interiors requires strategic structural solutions, from long-span beams to concealed supports.
Seamless indoor-outdoor transitions: Wall-to-ceiling glass doors, retractable window walls, and flush floor thresholds are frequently specified to blur the lines between interior spaces and the natural surroundings. These features require precise coordination between architectural details and structural engineering to ensure both aesthetic appeal and resilience to wind loads.
Quiet, comfortable interiors: High-end finishes and quiet environments are essential in luxury homes. Tight structural tolerances and vibration control are key to preventing unwanted movement or sound transmission, especially in homes with lightweight framing or large spans.
Integration of high-performance systems: Sustainable design and energy efficiency are no longer optional—they’re expected. Whether it’s geothermal heating, advanced HVAC systems, or achieving low HERS ratings, mechanical systems need to be seamlessly integrated without compromising the architectural vision.
Realizing complex designs on challenging sites: Many premium Hamptons properties are located on environmentally sensitive or technically demanding sites—narrow lots, bluff tops, flood zones, and areas with poor soil or high groundwater. Architects are still aiming for expansive layouts, dramatic views, and integrated landscapes, which requires engineering strategies that respond to site constraints without limiting the architectural vision.
Collaborating with architects to meet these priorities is at the core of our engineering approach. We work closely during the design phase to understand the intent behind every detail, ensuring that our structural, civil, and mechanical solutions support the creation of homes that are as functional as they are beautiful.
Common Engineering Challenges & Solutions in Hamptons Residential Projects
Behind every successful high-end residence in the Hamptons is a carefully coordinated engineering strategy that brings the architect’s vision to life while addressing the region’s complex site and environmental conditions. From coastal wind loads to high groundwater tables, the East End presents a range of challenges that require thoughtful, site-specific solutions.
At DAE, we approach each project with a deep understanding of these unique factors—and a commitment to aligning our structural, civil, and mechanical designs with the priorities of modern Hamptons architecture. Here’s how thoughtful engineering supports and enhances architectural priorities across each discipline.
Hamptons Structural Engineering: Balancing Aesthetics and Performance
In modern Hamptons residential architecture, structural engineering plays a key role in delivering the design intent without compromising performance or comfort. Architects are prioritizing expansive open floorplans, soaring ceiling heights, and refined finishes that demand precision and stability. Homeowners, in turn, expect quiet, solid-feeling spaces that reflect the quality of their investment. Achieving these goals requires structural solutions that are as sophisticated as the architecture itself.
Architectural Priorities Driving Structural Solutions
For high-end residential projects in the Hamptons, architects are consistently pushing the boundaries of design. At DAE, we frequently collaborate with design teams to address the structural considerations that come with these priorities. Some of the most common include:
Higher-than-normal finishes that are sensitive to movement: Luxury materials like stone, tile, and glass demand a structure with minimal movement. Even small deflections can lead to visible cracks or misalignments over time.
Desire for quieter, more solid-feeling homes: Homeowners expect a sense of permanence and quality. Limiting floor vibration and deflection is critical to delivering the quiet, stable environment associated with luxury homes.
Tighter tolerances to support premium finishes: Complex architectural elements—such as recessed showers, flush transitions, and detailed millwork—leave little room for structural error. Precision in framing and alignment ensures these details come together seamlessly.
Maximizing ceiling heights and open interior spaces: The demand for large, open living spaces with vaulted ceilings requires structural systems that can span greater distances while maintaining strength and stability.
Integration of complex architectural details: Features like deep shade pockets, oversized glazing, and cantilevered sections are common in modern Hamptons homes. These details require thoughtful coordination between architectural and structural teams to ensure feasibility and performance.
Addressing Structural Challenges on the East End of Long Island
Translating these architectural ambitions into reality requires a nuanced understanding of the region’s site conditions and environmental factors. Below are some of the most common structural challenges we address on East End residential projects—and the solutions we implement.
Foundation Stability in Poor Soils
Many Hamptons sites—especially along the coastline—feature sandy or organic soils with poor bearing capacity. On these properties, conventional foundations aren’t enough. Deep pile foundation systems, such as timber piles or helical piles, are often the best solution. These systems transfer the building’s load to deeper, more stable strata below the surface, preventing settlement and ensuring long-term structural integrity. For homes with large footprints or those incorporating basements, the design of these pile systems requires careful coordination to accommodate both structural loads and site constraints.
Building in Flood Zones and Managing Groundwater
A large portion of Hamptons properties lie within FEMA flood zones, where raising the house above the base flood elevation isn’t just recommended—it’s required. Elevating the structure reduces the risk of damage from coastal flooding and storm surge, which are common concerns in these areas. In most cases, this means supporting the home on piles, lifting the primary living spaces safely above potential floodwaters.
At the lower level, breakaway walls are often incorporated into the design. These non-structural walls are intended to give way in a flood event, allowing water to flow through rather than exerting pressure on the structure. By releasing under force, they help protect the integrity of the elevated home and its foundation.
But elevation alone doesn’t resolve every site condition. High groundwater is also a common challenge, especially on lots where homeowners want basements for mechanical rooms or additional living space. In these cases, basement designs need to resist hydrostatic pressure. That typically means reinforced concrete walls, waterproofing membranes, and drainage systems that manage water around—and under—the structure. These measures are essential to maintaining a dry, functional space below grade.
Spanning Large, Open Spaces
The preference for open floorplans and vaulted ceilings creates additional demands on the structure. Long spans, wide openings, and minimal visible supports require more than conventional wood framing. Often, projects call for engineered wood beams (LVLs), steel flitch plates, or full steel framing to handle the loads across large spaces.
But long spans introduce more than just structural load—they also increase the potential for deflection. In high-end homes, finishes like stone flooring, custom millwork, and flush glazing systems demand tight tolerances. Excessive movement, even within code-allowed limits, can lead to cracked finishes or noticeable shifts over time. The structural design needs to prioritize rigidity to protect the integrity of these materials.
Resisting Coastal Wind Loads
Wind is another constant factor, particularly for properties with expansive glass facades and minimal solid walls. These designs challenge lateral stability, especially in exposed locations where wind pressures can be significant. To counteract these forces, structural systems must provide resistance to lateral loads—essentially preventing the building from swaying or shifting under wind pressure.
Shear walls, moment frames, and proprietary systems like Simpson Strong-Walls are often integrated into the structure to resist these forces. Shear walls work by transferring lateral loads down to the foundation, creating a stiff, solid plane that limits movement. Steel moment frames use rigid connections between beams and columns to resist bending and lateral displacement, allowing for larger openings without sacrificing stability. Systems like Simpson Strong-Walls provide pre-engineered solutions that combine high lateral resistance with the flexibility to accommodate larger window and door openings.
Placement is key—these elements need to be coordinated with window locations, interior layouts, and architectural features to maintain the home’s design intent without compromising performance.
Hamptons Civil Engineering: Maximizing Sites and Meeting Complex Regulations on Long Island
Civil engineering plays a critical role in the successful execution of high-end residential projects in the Hamptons. Beyond providing the essential infrastructure—water, septic, drainage—civil design shapes how a property functions and feels. On many East End sites, the challenge is not just technical, but spatial: how to fit extensive programs, luxury amenities, and expansive landscapes on lots with significant environmental and regulatory constraints.
Architectural Priorities Driving Civil Engineering Solutions
For projects in the Hamptons, civil engineering decisions are often driven by ambitious design programs and the need to integrate systems seamlessly with the landscape. These priorities typically include:
Fitting extensive programs on constrained lots: Many homes feature multiple structures, swimming pools, patios, retaining walls, and extensive utility systems. All of this needs to fit on a site without crowding or compromising design.
Seamless integration of landscape and site systems: Retaining walls, drainage systems, and septic components must be designed so they complement the landscape, rather than dominate it. A clean, cohesive aesthetic requires careful planning.
Navigating complex permitting requirements without compromising design intent: Projects must meet stringent Suffolk County Department of Health (SCDOH) and environmental regulations. Civil engineering solutions need to balance regulatory compliance with the architect’s vision for the property.
Common Civil Challenges and How They’re Addressed
East End sites often bring difficult environmental conditions and strict regulatory frameworks. Below are a few of the most common civil challenges and the strategies used to overcome them.
Meeting Suffolk County Department of Health (SCDOH) Requirements
Many Hamptons properties require onsite wastewater treatment systems, and recent updates to SCDOH regulations have raised the bar for septic system design. The county now mandates the use of Innovative/Alternative (I/A) systems to reduce nitrogen discharge, particularly near wetlands and groundwater-sensitive areas.
These systems require careful design and permitting. Working within SCDOH guidelines while accommodating site constraints—such as lot size, proximity to wells, and neighboring properties—requires a detailed understanding of both the code and the approval process. On tight sites, septic systems are often located beneath driveways or parking spaces, triggering HS-20 loading requirements for traffic-bearing surfaces. This adds another layer of civil design coordination, requiring structural consideration to ensure tanks and chambers can support vehicular loads. Early coordination and precise engineering are key to ensuring these systems are integrated efficiently without delaying approvals or impacting the project timeline.
Managing High Groundwater and Poor Draining Soils
Many Hamptons properties face a combination of high water tables and poorly draining soils, both of which can complicate wastewater management and site grading strategies.
Wastewater Management Near Sensitive Environments
High groundwater tables and proximity to wetlands or neighboring wells create challenges for septic system placement and function. To ensure proper treatment and prevent buoyancy issues, shallow leaching fields are often used. The same site conditions often impact drainage design as well, requiring shallow stormwater solutions such as galleys, Cultec chambers, or gravel beds. These systems are designed to function within limited vertical clearance by maximizing horizontal storage and infiltration capacity. When groundwater is particularly high, sSeptic tanks may also require anti-buoyancy measures—such as concrete deadman anchors or weighted designs—to keep them stable ifwhen groundwater levels rise. These strategies help maintain system performance while protecting surrounding ecosystems.
Site Drainage and Grading in Poor Soils
Many Hamptons sites feature soils with low permeability, which can lead to drainage issues and standing water if not properly addressed. Where infiltration is limited, strategies such as over-excavation—removing poor soils and replacing them with more permeable material—are often implemented. In some cases, Pressurized Shallow Drain Fields (PSD) can serve as an alternative to deep leaching systems, avoiding the need for 50- to 100-foot excavations depending on percolation test results. Preliminary Site Design (PSD) planning is also essential to evaluate drainage capacity early in the process. These approachesis supportallows for the integration of subsurface drainage systems and grading strategies that manage stormwater effectively without compromising the intent or aesthetics of the site designlandscape design.
Hamptons Mechanical Engineering: Comfort, Control, and Clean Integration
In high-end Hamptons homes, mechanical systems are expected to do more than just function—they need to deliver invisible comfort, energy efficiency, and remain discreet within the architectural context. MEP engineering plays a central role in achieving the performance standards and environmental responsiveness expected in these residences, particularly as architectural designs trend toward open volumes, extensive glazing, and highly insulated envelopes.
Architectural Priorities Driving MEP Engineering Solutions
MEP design in luxury homes is often shaped by a blend of performance expectations and architectural intent. Some of the most common priorities include:
Achieving luxury comfort and high-performance climate control: Consistent temperatures, quiet operation, and responsive zoning are baseline expectations in high-end residences.
Managing heating and cooling in large homes with extensive glazing: High glass-to-wall ratios increase solar gain and heat loss, requiring careful planning to ensure thermal comfort throughout the home.
Humidity and condensation control for both comfort and material preservation: In tight, well-insulated homes, humidity management is critical to preventing condensation on windows and protecting sensitive finishes.
Well-organized mechanical rooms that reflect the home’s overall aesthetic: Mechanical spaces are often visible during walkthroughs or integrated into finished areas—neat, accessible layouts are part of the design conversation.
Common MEP Challenges—and How They’re Addressed
Mechanical, electrical, and plumbing systems must be designed to work seamlessly with the architecture while meeting strict energy codes and performance demands. Below are key challenges and how they’re typically resolved on East End projects.
Meeting HERS Ratings in Large, Glazed Homes
Hamptons homes tend to be expansive and feature significant glazing—both of which can make it difficult to meet energy efficiency requirements, including low HERS (Home Energy Rating System) ratings.
To address this, energy modeling is integrated early in the design process, allowing MEP engineers to evaluate various system configurations and envelope strategies. High-efficiency HVAC systems, geothermal or air-source heat pumps, and solar-ready infrastructure are often part of the design, helping reduce energy loads while preserving the architectural form. The goal is a system that delivers performance without forcing compromises to the layout or aesthetics of the home.
Delivering Comfort at Scale
Maintaining consistent comfort in large, complex residences is no small task. With sprawling floorplans, multi-zone living, and a demand for near-invisible mechanical presence, systems must be both robust and precisely calibrated.
Radiant heating is frequently used for its even heat distribution and quiet operation. Hot water recirculation loops reduce wait times and improve efficiency, particularly in homes with multiple bathrooms spread across multiple levels. Proper HVAC sizing, duct routing, and zone control ensure comfort is consistent from one end of the home to the other, with minimal visual impact.
Humidity Control and Indoor Air Quality
With the tight building envelopes typical of high-performance construction, moisture control becomes a critical part of mechanical design. Homes with large window walls are especially prone to condensation issues, which can affect both comfort and material longevity.
To mitigate this, dehumidification systems are often integrated directly into the HVAC system, maintaining indoor humidity within a safe, comfortable range. Balanced ventilation—through systems like ERVs (energy recovery ventilators)—ensures fresh air circulation without sacrificing energy efficiency. Vapor control strategies are also considered at the envelope level to manage condensation risk holistically.
Why Experience Matters
Delivering successful residential projects in the Hamptons requires more than technical skill—it demands a deep understanding of the region’s environmental conditions, permitting landscape, and design expectations. From managing groundwater on tight sites to navigating Suffolk County Health Department approvals or integrating mechanical systems into architecturally ambitious structures, each challenge requires a solution tailored to both the site and the design vision.
At DiLandro Andrews Engineering, we work closely with architects, builders, and developers to anticipate issues early, streamline coordination, and ensure every detail—from the foundation to the mechanical room—supports the integrity of the overall design. With local insight and a multidisciplinary approach, we help turn complex projects into cohesive, high-performing homes that stand up to the unique demands—and elevated expectations—of luxury custom residences on the East End.
To see how these principles translate into built work, explore our portfolio of residential projects across the East End.